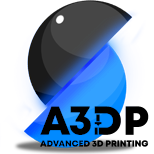
https://github.com/robthide37/A3dp-Slicer
https://github.com/robthide37/A3dp-Slicer/releases
Patrons please let me know what features you want in the slicer .
Biggest new feature is independent Fan control for Idex and or multiple Hotends.

https://github.com/robthide37/A3dp-Slicer
https://github.com/robthide37/A3dp-Slicer/releases
Patrons please let me know what features you want in the slicer .
Biggest new feature is independent Fan control for Idex and or multiple Hotends.
I will add more info over the next few days but this shows how to setup the Euclid also in the Troodon case with an additional endstop on the 6 pin header. The double connection is required to allow us to be able to home with having an additional physical z endstop. This will allow the Euclid to replace a Bltouch without any additional endstops.
I have gotten feedback and done a few installs on patrons machines. Its at the point wherre last step is a guide then will be able to allow purchase through the store.
I can now proudly say that A3dp has a complete solution for upgrading to servos on a 3d printer. This tuning software allows you to tweak the current and position loop or set it to auto-tune. You can also view real-time feedback from the encoder and controller. Also you are able to access anti vibration loops with phase shifting so if you have large equipment that has resonance or an imbalanced shaft it can be corrected in software.
These motors are able to expose the limits in most control boards which is now pushing others to create a custom version of Klipper that increases possible step rate by many orders of magnitude. This will allow us to slowly start adding more features and higher levels of performance on top of what we can already achieve . As an example we can currently run the motors at 8192 steps per rotation “the motors technically can run whatever you want but their would be little reason to go above 16384 since that is the hardware resolution of the encoder” if we want extreme quality or 4096 if we want to go over a meter per second. At 8192 we are accurate to .00488 of a mm with a 20t pulley and .0039 with a 16t or at 4096 both pulley sizes get us under .01 compared to a .9 stepper getting us .1mm with a 20t “if we pretend that their is 0 lag and we have 0 resistance in the system ”
You may need to install net Framework 3.5 which you can press windows key then type add or remove windows features and make sure net framework 3.5 is selected .
Patrons please let me know what features you want in the slicer . We just added individual PA control for every accel value and better variable layer height control plus a few smaller tweaks. Most stuff will eventually go to Super Slicer as well but some stuff will be staying as A3dp exclusive. Especially the profiles for Modix and Troodon and then toolchanger and index support along with Stablebot support for LukeLabs machines
We Can now adjust by percentage or absolute PA for diff types of extrusion which is super important . This also make handling things like two hotends easy to to do without having to write macros.
As many of you know their is not to many choices for Tungsten Carbide nozzles , especially in Volcano size . So A3dp now is carrying our own line of nozzles along side the standard Takoto brass nozzles . I also am thinking of getting standard size Tungsten Carbide nozzles made to but am not sure if the market needs it since those tend to be easier to source. Anyway I used one of them in my recent 1023mms live stream and also at 600mms for the fox benchy . I will be doing a comparison between a few different nozzles and want to get some real data on the actual limits since it seems you can flow a lot more on a .4 than people think.
Purchase link below
As many know the hosting company i was using somehow lost all their data and this included backups and so on. Now i am using amazon servers and doing offline backups even though everyone claims the cloud is safe “apparently not for me ” Anyway point is Me JAke and Theodore are going to try and fix all the broken posts over the next week.
Ill start this with saying that if anyone has info on this please come forward as their seems to be very few resources and they are all cryptic. Anyway i have found all the trinamic whitepapers to be very helpful and over the past year hae tested and experimented to the point where i feel i have a decent grasp on how this works.
this is a list of the calculators and guides.
https://www.trinamic.com/support/app-notes/
This is a list of specs that i will keep adding to or if you have any motors you want added comment below and if you have any spec sheets feel free to please comment here or on gihub.
https://github.com/robthide37/components/blob/master/Helpdocs/stepper%20specs
How to use
So i wanted to show the new version of the gantry carriage. The rest of the gantry is the same except for slight tweak that applies to the 300 only . I ordered 20 more of the tha carriage piece encase anyone wants to convert to the new modular design. This adds another way to mount the mosquito and also the mosquito magnum plus now shoudl be possible “haven’t been able to test in real life yet ” Also adds takoto compatibility and makes it possible to quick-change the hotend and extruder. The best part of this is i plan on having future upgrades available that we can simply swap the plate with 2 bolts and then also have the chance to try and make a toolchange setup without having t5o redo anything else . Theodore has also asked me to make a 9mm belt version so i had already drawn it up and i will make a small amount of 9mm belt setups for those that want to run large servos or something where we may see an advantage. I will test that soon though. Will be doing a giveaway as well
This is a 3d view that can be exploded showing the install.
password is a3dp
This is all needed files for the install https://drive.google.com/drive/folders/1Z4x9JJPxMVS33Lny1YkzpYVabQZxyF_G?usp=sharin
First step is to make sure you have all the parts needed for the install including stls from the other post.
Tools needed
Remove the front and side lower panels and it is helpful to remove the acrylic panels to. Then remove the black acrylic surround that is around the bed. Be mindful to remove the bracket that holds the z cable chain otherwise you will have a very hard time removing the surround
Next remove the bed by removing the 4 m5 allen bolts . alternatively you can place the printer on its side and remove the bottom
The first thing is to make sure that you have plenty of time and have printed all needed parts which is the
Next is required tools and required parts
The first thing i recommend to do is the front three pieces which give the largest gain. That is the carriage and the x to y mounts. You will need to act like doing a dde install and open the cable chain up including the Z chain.
Remove the back bracket that holds the z chain from moving and also prevents the bed surround from lifting. Then remove the 4 screws that hold the bed surround down and remove the bed surround to make your life easier.
Now remove z links so that the 400 has approx 31 to 32 and the 300 has 23 to 24 . then pull any slack out of the cables making sure not to stretch or disconnect anything below . You may need to cut zip ties. At this point remove the xy cable chain and make a 19 link length for the 400 and the 300 can be 16 to 19 links as their is more slack . This will be the y chain unless using new. use the old t nuts to mount the cable chain to the y extrusion and then leave for now
At this time remove the 4 screws on the bottom of each guide on the y extrusions to drop the old x bar away. Now mount the new x to y joints almost finger tight . Then take the double t nut plates and use them to mount the rail still not tight . now mount the x to y joint that say a3dp on it and mount he carriage to the guide. At this point you can lift up on the rail a little and tighten the inner bolts to the tnut plate hand tight then release the rail and now tighten the outer bolts to the t nut plate firm but not crazy , go back and do the same for the first set and now move gantry forward and back and then tighten the bolts holding the x to y arms to the y rails.
Now you can mount the carriage cable chain mount and if you printed a spar mount that as well . You can now also run the cable chain to the carriage and mount the loose ends of the both cable chains to their respective locations.
Remove the extra idler from the front tensioner brackets and run the belt around the z belts as shown in the pictures above . Install the idlers on the new arms using the stock spacer underneath and nothing above. At this point attach belts to the carriage as it is much easier before hotend is installed.
Mount the y endstop mount trigger and mount your x endstop to the a3dp x to y cable chain mount. You can now install the hotend ,fans and extruder.
I will be completing a video shortly and will refine this with feedback but wanted to get a basic idea of what to do written down as a starting point so feel free to ask questions and i will edit this accordingly.
The motor mounts are more difficult but not by much . You need to setup the pins ahead of time so sand the pins or some said to use a freezer and place the idlers on the pins as shown in the pics. Now remove the old belt retainer clips and the old rear brackets. You need to install the 1mm spacers on the bottom of the extrusions in-between them and the new brackets. You will mount the motor with the button head screws supplied 3 to a motor. You need to take care not to lose the old hardware. ” seems some newer printers have thicker stock washers I am looking for a link if anyone wants to get proper replacements for the rear stack” Don’t run the belt until the last step for this install as it is much easier to just snake it through and it helps to remove rear panel so you disconnect power and unplug the spade connectors from t he block on the back . You can do this without removing the back panel and just removing the sides instead. Use the longer m5 bolts to replace the stock 12mm bolts that go thought the z mounts and the mounts as they are to short for stock let alone an additional mm for the new spacer. Install spacers under the stock front mounts, Install center t nut bolts loosely and run gantry forward and back then tighten them to avoid racking. Now you may run belts and make sure the tensioner set screws in front are out all the way. Take care to have some tension on belts but not much and then clamp with zip ties or printed retainers. Now you may tension taking care to keep gantry square with tension being equal. Refer to video on belt tension to understand if confused.
cd klipper_config
git clone
https://github.com/robthide37/components.git
[update_manager client components]
type: git_repo
origin: https://github.com/robthide37/components.git
path: ~/klipper_config/components
Delete your existing directory and extract this into it its the newest version with hardware accel back on. I was going crazy i actually installed windows again cause thought was my computer. When i made a platter of like 4 orbiters or 30 cable chain links i could not even get 1 fps and then i couldnt even type while it was open and i running a 5950x with 64gb ram right now so i was really at a loss. But try the gcode viewer or slice preview then do this and try again .
you will not lose your profiles as they are stored in the USERS/AppData/roaming then i think superslicer ALPHA folder but anyway you get the point