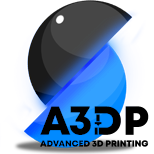
https://github.com/robthide37/A3dp-Slicer
https://github.com/robthide37/A3dp-Slicer/releases
Patrons please let me know what features you want in the slicer .
Biggest new feature is independent Fan control for Idex and or multiple Hotends.

https://github.com/robthide37/A3dp-Slicer
https://github.com/robthide37/A3dp-Slicer/releases
Patrons please let me know what features you want in the slicer .
Biggest new feature is independent Fan control for Idex and or multiple Hotends.
I will add more info over the next few days but this shows how to setup the Euclid also in the Troodon case with an additional endstop on the 6 pin header. The double connection is required to allow us to be able to home with having an additional physical z endstop. This will allow the Euclid to replace a Bltouch without any additional endstops.
I have gotten feedback and done a few installs on patrons machines. Its at the point wherre last step is a guide then will be able to allow purchase through the store.
I can now proudly say that A3dp has a complete solution for upgrading to servos on a 3d printer. This tuning software allows you to tweak the current and position loop or set it to auto-tune. You can also view real-time feedback from the encoder and controller. Also you are able to access anti vibration loops with phase shifting so if you have large equipment that has resonance or an imbalanced shaft it can be corrected in software.
These motors are able to expose the limits in most control boards which is now pushing others to create a custom version of Klipper that increases possible step rate by many orders of magnitude. This will allow us to slowly start adding more features and higher levels of performance on top of what we can already achieve . As an example we can currently run the motors at 8192 steps per rotation “the motors technically can run whatever you want but their would be little reason to go above 16384 since that is the hardware resolution of the encoder” if we want extreme quality or 4096 if we want to go over a meter per second. At 8192 we are accurate to .00488 of a mm with a 20t pulley and .0039 with a 16t or at 4096 both pulley sizes get us under .01 compared to a .9 stepper getting us .1mm with a 20t “if we pretend that their is 0 lag and we have 0 resistance in the system ”
You may need to install net Framework 3.5 which you can press windows key then type add or remove windows features and make sure net framework 3.5 is selected .
Patrons please let me know what features you want in the slicer . We just added individual PA control for every accel value and better variable layer height control plus a few smaller tweaks. Most stuff will eventually go to Super Slicer as well but some stuff will be staying as A3dp exclusive. Especially the profiles for Modix and Troodon and then toolchanger and index support along with Stablebot support for LukeLabs machines
We Can now adjust by percentage or absolute PA for diff types of extrusion which is super important . This also make handling things like two hotends easy to to do without having to write macros.
These are password protected and the password is all lower-case:
a3dp
Here is an embedded viewer of the 300 A3DP Troodon in all of it’s glory via Fusion 360 Cloud Viewer.
Link to the model in the Fusion 360 cloud:
https://icloud14783.autodesk360.com/shares/public/SH56a43QTfd62c1cd9686686412699ae42ba?mode=embed
It still mounts in the front-right corner as with the one we recommended before.
For assembly, start by plugging in the pi cable into the Pi Cam, place the cam in the red piece (as pictured above) then snap the yellow piece on. Next you will need a M3x20mm bolt to assemble the gray bottom mount to the yellow back plate. Finally, you will need a M4x12mm bolt and a 3030 hammer/ or t-nut for mounting to the front-right extrusion on your Troodon.
Please see the attached screen shot for slicer print orientation. I would suggest 0.16-0.2mm layers, ABS material for easier breakaway supports. The rear face may require some light sanding.
Inspired by the following projects:
Front housing: https://www.thingiverse.com/thing:4695691
Back cover: https://www.thingiverse.com/thing:2746186
This solution came about because I have yet to find a nice clean, customizable solution for storing E3D v6 style nozzles. That is a thing of the past. I would like to introduce our Nozzle Storage Box.
The intention here is that the Nozzle Insert is customizable for your application. It prints with no support in 4 pieces. We are providing all of the STL files, F3D and a STEP file for those who prefer to customize their box further.
I wanted to take a few minutes to upload what Rob and I are calling the “Ultimate” Orbiter. Just so everyone knows, this design I did completely from the ground up making dozens of minute modifications for easier FDM-ability thus it is completely our own intellectual property.
The special sauce that gives our design a huge advantage over the original Orbiter designed by Lorincz are as follows:
There are two versions of the housing:
1.) 14x14mm Bearings, this will match up for those that bought the “Formbot Troodon DDE Upgrade” kit from Jake/Tom/Peter on Cults3D.
2.) 14x16mm Bearings, this matches the “OEM” Formbot/Vivedino DDE kit that can be purchased or came installed on your Troodon.
Rob & Jake both have hundreds of hours testing this new orbiter and we are ready for you to give it a shot for yourself
If you have any question, please drop us a line in the comments!
As many of you know their is not to many choices for Tungsten Carbide nozzles , especially in Volcano size . So A3dp now is carrying our own line of nozzles along side the standard Takoto brass nozzles . I also am thinking of getting standard size Tungsten Carbide nozzles made to but am not sure if the market needs it since those tend to be easier to source. Anyway I used one of them in my recent 1023mms live stream and also at 600mms for the fox benchy . I will be doing a comparison between a few different nozzles and want to get some real data on the actual limits since it seems you can flow a lot more on a .4 than people think.
Purchase link below
Hey Everyone,
Per a request from Facebook, I am sharing the redux I did on the SailFin extruder (OG design credit to CroXY3D)
I am leaving a link to the shared files here where you can access them as well as an Exploded Assy View video for assembly, follow the same instructions recommended for the Original SailFin.
I have been running this for about 25hr, CF & GF filaments have been fine as has ASA/ABS, I have yet to do flexibles but I would expect the same great performance as our A3DP Orbiter as it has the same fully constrained filament path.
If y’all have any feedback, let me know on Facebook.
Link to the STLs, pictures, & video
This is the A3DP Troodon 300 CAD Model, it is special sharing version of the model, but is not downloadable.
Inside of the viewer window you can do quite alot but here are some highlights of the most important:
1.) Explode the model (3 Planes Icon)
2.) Measure parts for real-world comparisons (Ruler Icon)
3.) Hide & Isolate Parts / Sub-assemblies to see just what you want
Lastly, I also took the time to rename all of the parts in the design tree (Top-Left corner, look for a Cube & Click on it)
As many know the hosting company i was using somehow lost all their data and this included backups and so on. Now i am using amazon servers and doing offline backups even though everyone claims the cloud is safe “apparently not for me ” Anyway point is Me JAke and Theodore are going to try and fix all the broken posts over the next week.
This is a guide for printing a turnkey mount for an ElecLabs 5″ Klipper Screen, this is not a full guide for installing the mount. That being said, here is a link to the Klipper Screen documentation. Big shout out to those guys, this screens rocks.
Here is where I used to purchase this screen.
Rather than charging for this before you try it, I would rather use this as an Honor System. I’m more concerned with growth than money but money is a necesarry evil for coninued development. If you found it useful and would like to see more like it, please consider donating to the designer with the “Tip the Designer” button below:
Future Projects I am considering:
UPDATE: had an issue with the parts falling over when printed upright, I added some “forced” supports in the 3D CAD model to prevent this and it works. Just be sure to use the .3MF file attached below and print with a large brim and speed of 80mm/s. They turned out very nice now.
Have you ever wished that your Troodon door would stay open rather than slamming you in the elbow when your reaching in to do something to the machine? OR wanted to have a quick way to remove the door with our messing with the door alignment and/or not need any tools to take the door off?
Today is your lucky day!
I have composed 2 different version of this hinge, but let me explain how it works first.
Hey folks, just wanted to share a couple bed textures I whipped up in MS Publisher
So i wanted to show the new version of the gantry carriage. The rest of the gantry is the same except for slight tweak that applies to the 300 only . I ordered 20 more of the tha carriage piece encase anyone wants to convert to the new modular design. This adds another way to mount the mosquito and also the mosquito magnum plus now shoudl be possible “haven’t been able to test in real life yet ” Also adds takoto compatibility and makes it possible to quick-change the hotend and extruder. The best part of this is i plan on having future upgrades available that we can simply swap the plate with 2 bolts and then also have the chance to try and make a toolchange setup without having t5o redo anything else . Theodore has also asked me to make a 9mm belt version so i had already drawn it up and i will make a small amount ย of 9mm belt setups for those that want to run large servos or something where we may see an advantage. I will test that soon though. Will be doing a giveaway as well